What is a PDI check?

Before you take delivery of your new lease vehicle from Nationwide Vehicle Contracts, it will have to go through a pre-delivery inspection, also known as a PDI check.
But what exactly is a PDI check, how long does it take, and will it affect your estimated delivery date?
To help explain the PDI process, Nationwide Vehicle Contracts has put together a short guide to answer all these questions and more. We discuss:
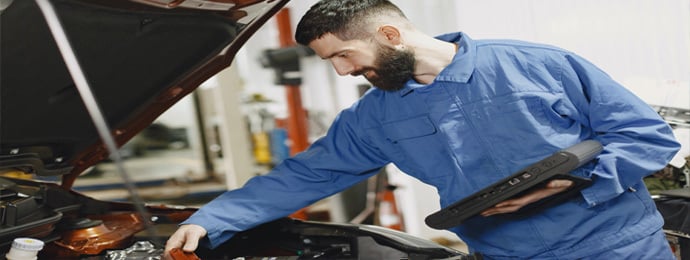
A PDI check is a rigorous inspection of your new lease vehicle before it’s delivered. It is an important and final check, carried out by the supplier, to ensure that the car is in full working order and safe to drive.
The check is designed to highlight any issues with the car which might have been missed at the factory or sustained during transportation.
These can include cosmetic issues, such as scratches on the paintwork, to mechanical problems, like warning lights on the dashboard.
During the check, a technician runs through a series of different checks on the car. Each manufacturer has its own checklist, but in general, six key sections are typically checked:
Pre-delivery inspection checklist
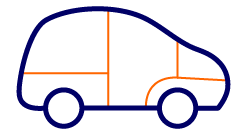
1. Vehicle exterior
Firstly, the vehicle's body is examined, including the bonnet, door panels, alloy wheels and roof. The inspection agent is looking for any exterior damage, such as scratches to the paintwork, dents on the bodywork, scuffs to the alloy wheels or missing parts. An inspection of the exterior lights also takes place to ensure they are all working.
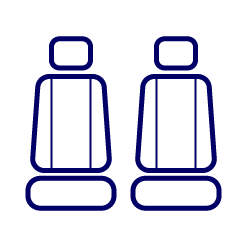
2. Vehicle interior
The inspection agent then moves onto the interior, checking the upholstery to ensure there are no rips or tears in the seating or door panels. Features on the vehicle's console and dashboard are also tested, from the indicators and windscreen wipers to the infotainment system and USB ports.
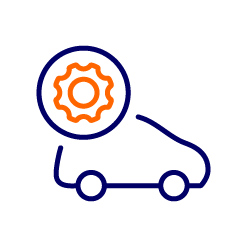
3. Engine compartment
The mechanic then inspects the engine components for visual flaws and irregular noises. All fluids, including washer, coolant and brake, are checked, and the battery is checked for sufficient charge and to ensure it is fully operational.
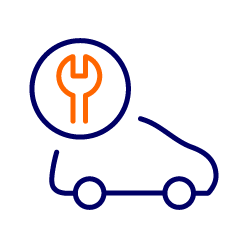
4. Vehicle underside
Components are visually inspected to ensure there are no visual defects such as holes or tears on electrical lines, hoses, exhaust systems, and suspension parts.
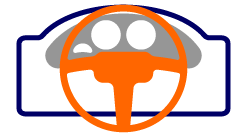
5. Road test
Often, a short road test will take place to listen or feel for any problems with the engine, transmission, brakes, clutch, cruise control, steering, lane departure warning, and air suspension, if present. The computer is scanned for any diagnostic error codes.
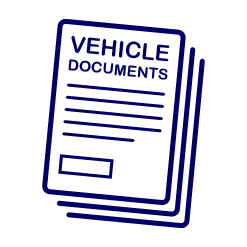
6. Final preparation
The last step is to remove all protective coverings and ensure the vehicle's number plates are placed on the car. A PDI also includes checking the owner's manual, service book, and warranty guide are present to be handed over to the customer.
Other things that may be inspected on a PDI check include:
- Original and spare keys are present and working
- Locking wheel nuts are present (if applicable)
- Owner manual and service book are present (if applicable)
- All tyres are legal (including spare), and tool kit is present
- All lights, horn, indicators and warning lights are working
- Any accessories specified (such as floor mats, tow bar etc.) are fitted
- Vehicle Chassis Number and Registration Plate match paperwork
Many dealers will get the car valeted before delivery, however it is worth noting that many vehicles are then driven to the customer's handover address, so road dirt or traffic film may be visible on the exterior.
For more information, check out our guide, Taking Delivery of Your New Lease Car.
The vehicle's manufacturer or supplying dealership is responsible for completing all PDI checks. A trained technician carries out a series of inspections. These are usually conducted at the dealership or at a central holding compound where the car is held.
Note: These checks are not completed by Nationwide Vehicle Contracts.
PDI times can vary depending on the manufacturer and the level of detail requested. The average PDI time is one to two hours, but some vehicles can take up to five hours to complete.
For your delivery date not to be affected by any issues that need fixing before delivery, suppliers require at least five working days' notice to ensure they have enough time to fix any issues or repairs that may be required.
Generally, a PDI check should not affect the delivery date of your vehicle. However, on rare occasions, the dealer may ask for your delivery date to be rescheduled if a problem is found at inspection that may take longer to rectify.
It is important to note here that while delays to delivery can be frustrating, a PDI check aims to ensure the vehicle is safe to drive, so if you are affected by a delay due to an issue found at PDI, please be patient.
As soon as the problem has been rectified, our deliveries team will be back in touch to arrange a new delivery date at a day/time convenient to you.
“While delays caused by a PDI check are rare, they do happen from time to time, and when they do, it’s always with the customer’s safety in mind. We’d much rather postpone delivery by a day or two than hand over a vehicle that hasn’t met our quality standards.”

If a defect is found, the manufacturer will fix or amend the vehicle to the correct specification before it is allowed for delivery.
Many minor problems, such as scratches, scuffs or cosmetic issues, can be sorted at source, but mechanical problems, such as engine management issues may need a specialist, which can take longer.
A PDI check might sound just like another bit of car jargon, but it's far more valuable than that. It’s assurance that your lease car has been thoroughly checked, cleaned, and prepared before delivery.
For lease customers, you know the car has passed its final checks, setting the tone for a hassle-free driving experience.
Guide Information
Originally published: 19th July 2022
Last updated: 17th July 2025
Due to be reviewed: 16th July 2026